June 20, 2019
Successful data mining - the maritime sector’s golden nugget?
Shervin Younessi, Technical Manager of Royston Power Generation, explains how real time data synchronisation and big data analytics have an essential role in monitoring vessel energy efficiencies, reducing fuel consumption and controlling emissions.
With the digital evolution in the marine industry gathering pace to help tackle the challenge of new regulations and sustain more energy efficient fleet and vessel operations, ships of all types are becoming sophisticated sensor hubs.
Advanced sensor technology and sophisticated communication systems have come together and the benefit is considerably enhanced ship connectivity that now allows the telemetry of an extensive volume of operational data.
As a result, ‘big data’ marine platforms will increasingly have an enormous effect on how vessel owners and operators manage information and utilise real time analytics for ongoing performance monitoring to deliver operational benefits.
In particular, data synchronisation and analysis from multiple sources will inevitably enable operators to make more informed decisions faster and it will enhance vessel performance management in key areas such as fuel consumption, energy management, emissions control, machinery and equipment monitoring and route optimisation.
In this way data mining in the shipping industry will bring new knowledge and added value to assist with better decision making, asset monitoring and optimum utilisation of both the individual vessel and the entire fleet.
The challenge
Various on board sensors are already used to measure different aspects of ship performance, such as fuel flow, engine torque, RPM and power, as well as temperatures, pressures, electrical load and speed of the vessel.
In doing so, an unprecedented volume of vessel and engine data, not to mention weather, sea conditions and other external factors, is generated from different sources and in different formats. In fact it has been estimated that a modern ship generates for than 20 gigabytes of on-board data each day.
However, while this volume of information undoubtedly provides added value to the operator, without effective analysis it can also create serious challenges.
In particular, different sensors usually feed data into different monitoring systems that do not normally communicate with each other. It is also common for sensors to use different communication protocols including formats such as Ethernet, serial, CANbus, 4-20mA and others.
Large and complex data sets are therefore notoriously difficult to process and analyse using traditional processing techniques and applications.
The common hub
To overcome this problem, and as part of a programme that considers a systematic approach to whole vessel energy management, recent work has been undertaken on the development of standardised methodology to collect the raw data in real time – and successfully convert it into a format that is capable of enabling user functionality and decision making.
This common hub concept is capable of interfacing and integrating with existing and new sensor technology, converting numerous communication protocols into one data format. The hub is also capable of analysing, aggregating and bundling the vessel dataset for transmission to display stations located on board and onshore.
The hub incorporates a number of stages that utilise specially developed software capable of taking data from the various sensors and converting it into useful information.
The communications platform that achieves this involves ‘sensor containers’ with a filtering capability to remove stray and inconsistent data, a data aggregator to process the information and a database plugin module that stores the information ready for transmission onshore.
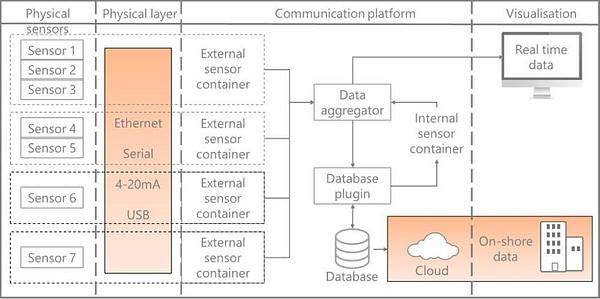
Data analysis in practice
To validate this system of data sources and collection, a series of tests have been undertaken on a range of vessels types including a tug, research vessel, OSV and a passenger ferry.
The tests involved the installation of the enginei energy management system to monitor real time fuel consumption, speed over ground, shaft power and location and other sensor measurements.
Different measurements and data flows were gathered during different types of vessel operations and activities, with the results from the tests being validated by comparison with original sea trial data for the vessels, technical specifications and theoretical calculations.
As a result a variety of datasets on fuel consumption and engine power and other operating parameters were gathered that enabled baseline engine efficiency measurements to be established.
For example, results from the speed tests enabled benchmarking curves to be developed for both specific fuel oil consumption and delivered power against speed that can be used as reference points for future measurements, taken, for example, after dry docking or engine maintenance work.
In addition, the data from the sensors also enabled a breakdown of energy flow throughout the whole vessel to be measured and used to calculate engine efficiency, as well as energy losses caused, typically, by heat and exhaust loss.
Quantifying energy losses in this way, as well as providing opportunities to improve operational performance, also encourages further investigation into on board energy recovery systems and the potential use of waste energy.
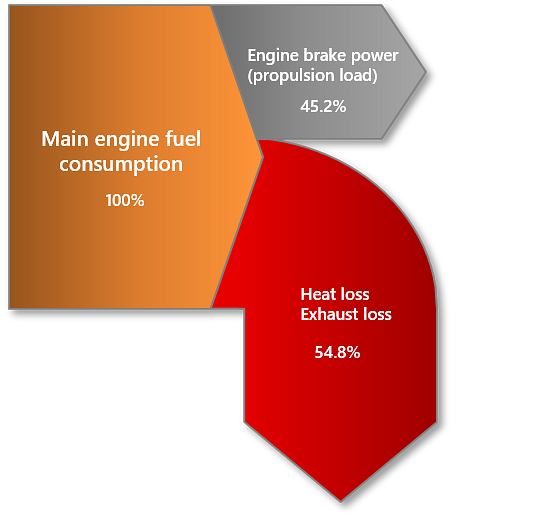
Additional analysis was also used to demonstrate the potential fuel cost savings available to operators by identifying the optimum speed for operation - one of the most commonly used strategies for fuel savings.
During the tests it was observed that the tug would travel at a high speed of 10-13 knots during transit, with an average of 11.5 knots and fuel consumption of 180 litre/hr. In comparison, using fuel consumption data produced during the speed test, at the determined optimum speed of 9.2 knots, the engine burns only 107 litres of fuel per hour – demonstrating a considerable saving in fuel cost with only a small reduction in average speed.
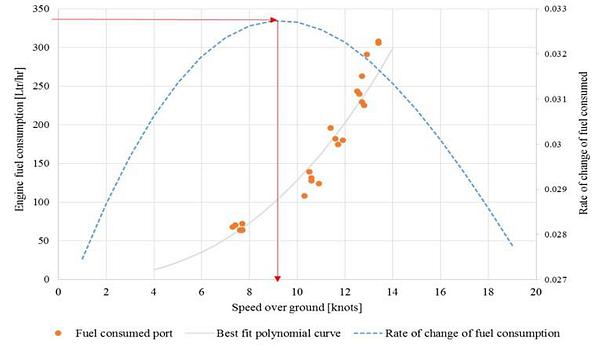
With the development and improvement of new sensor technologies and other measurement devices, data-centric applications are already having a considerable impact on the shipping industry.
This trend will only grow in importance and rely ever more heavily on the ability to accommodate and interpret large amounts of real time data to enable key operational decisions to be made.
Whole vessel energy management considerations utilising a common hub approach provide a solution to this problem and are already demonstrating the capability to analyse and aggregate data on board the vessel, as well as allowing for transmission and further interpretation onshore.
In this way, new on board data mining techniques provide a systematic means of helping vessel owners and operators come to terms with the key operational issues of improving performance, minimising vessel downtime and reducing harmful emissions.